Reducción de riesgos en la industria siderúrgica
La industria siderúrgica depende en gran medida de las transformaciones a alta temperatura para obtener el producto final. Los componentes son susceptibles a la corrosión, el desgaste y los problemas de integridad estructural. Además, la dureza del entorno plantea riesgos importantes, por lo que resulta difícil garantizar la seguridad del personal.
En octubre de 2023, Duferco Travi e Profilati puso en marcha un nuevo tren de laminación denominado Smart Beam Manufacturing (SBM) en San Zeno Naviglio, Brescia (Italia). Con una longitud de 500 m y una superficie de más de 78.000 m2, es el mayor tren de laminación de Italia, con una capacidad total de laminación de 700 K toneladas de productos largos. Diseñada para estar a la vanguardia de la sostenibilidad, la tecnología y la innovación, la planta funciona totalmente con energía renovable.algo que nos interesa mucho en Fortress , ya que funcionamos exclusivamente con fuentes de energía renovables y nuestro objetivo es tener cero emisiones netas de alcance 1 y 2 para 2028.
Gracias al gran trabajo realizado por LAS, nuestro Channel Partner en Italia, se ha confiado a Fortress la función de proteger al personal que trabaja en la flamante obra, proporcionando soluciones de seguridad para más de 100 puntos de acceso.
Afrontar los retos de las condiciones extremas
Para ser adecuados en las condiciones en las que funciona el tren de laminación (es decir, riesgo de impacto con piezas móviles pesadas, altas temperaturas que pueden alcanzar los 1250 °C), los productos de seguridad debían:
✅ Ser extremadamente resistente
✅ No tener cableado cerca de los puntos de acceso.
✅ Proporcionan protección en zonas extensas en las que los operarios pueden no ser siempre visibles.
Debido al riesgo de que el personal quedara atrapado, hubo que abordar la puesta en marcha inesperada. En este caso concreto, al no ser posible el cableado cerca de los puntos de acceso, las funciones de liberación de escape no eran viables. Además, dado que los cuadros eléctricos controlaban secciones específicas (cada una con varios puntos de acceso), era necesario un módulo que aplicara una lógica de liberación de llaves para permitir el acceso a los respectivos puntos de entrada al aislar la alimentación de los cuadros.
Fortress tenía la solución perfecta para responder a todos los requisitos mencionados en la mGard gama:
✅ Totalmente mecánico, sin necesidad de cables.
✅ enclavamientos de acero inoxidable aptos para entornos difíciles
✅ llave(s) con extracción forzada, de modo que el personal deba llevar consigo su llave de personal en la zona salvaguardada.
El uso de llaves de personal codificadas en Fortress mitigaba el riesgo de que el personal quedara encerrado en la zona protegida. Los guardapolvos con candado proporcionaban una protección adicional, dando al personal adicional que entraba en la zona protegida la posibilidad de aplicar candados personales en la cerradura, impidiendo que se cerrara el resguardo mientras se estaba dentro.
Otros beneficios importantes de Fortress fueron:
✅ la posibilidad de grabados y diferentes opciones de color en las teclas. Esto simplificó la gestión de las teclas y facilitó a los operarios saber qué tecla utilizar
✅ llave maestra a disposición del personal especializado (es decir, responsable de mantenimiento o director de obra) en caso de emergencia o problemas.
Productos electromecánicos para Funcionalidades adicionales
Para los puntos de acceso de una sección diferente del tren de laminación (zona fría, con condiciones menos exigentes, compatible con el cableado) se necesitaban lógicas, pulsadores y funciones específicas, como un liberación de escape .
Con la tGard gamaFortress ha podido ofrecer soluciones electromecánicas en un solo producto. De hecho, los productos tGard tienen un cuerpo metálico de 40 mm que puede alojar hasta 10 módulos, con la posibilidad de incluir pulsadores, lámparas, paradas de emergencia, etc.
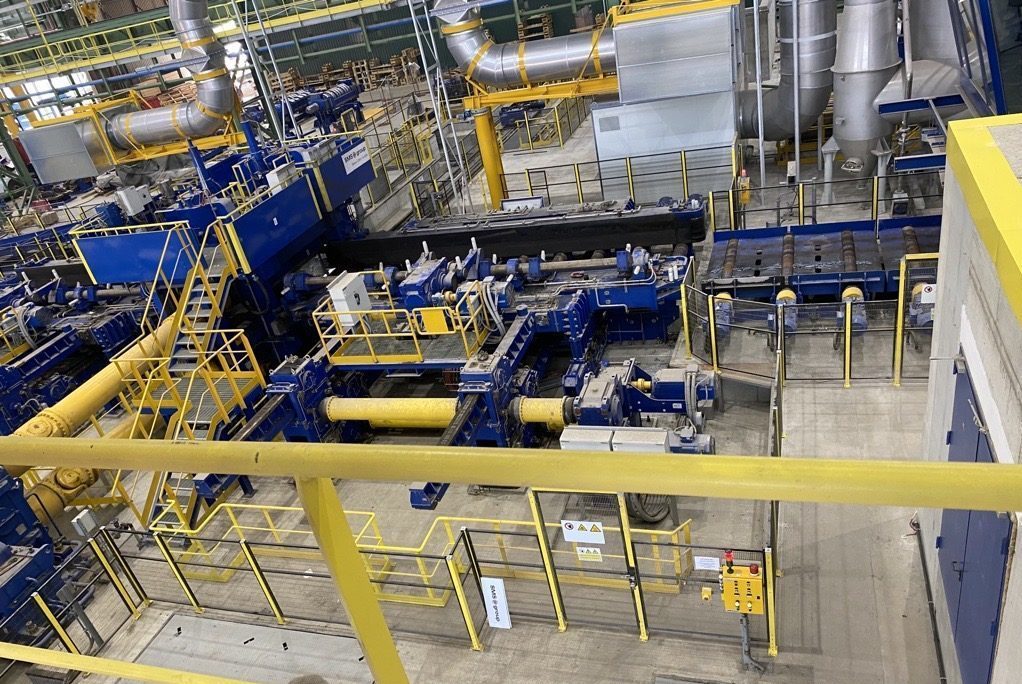
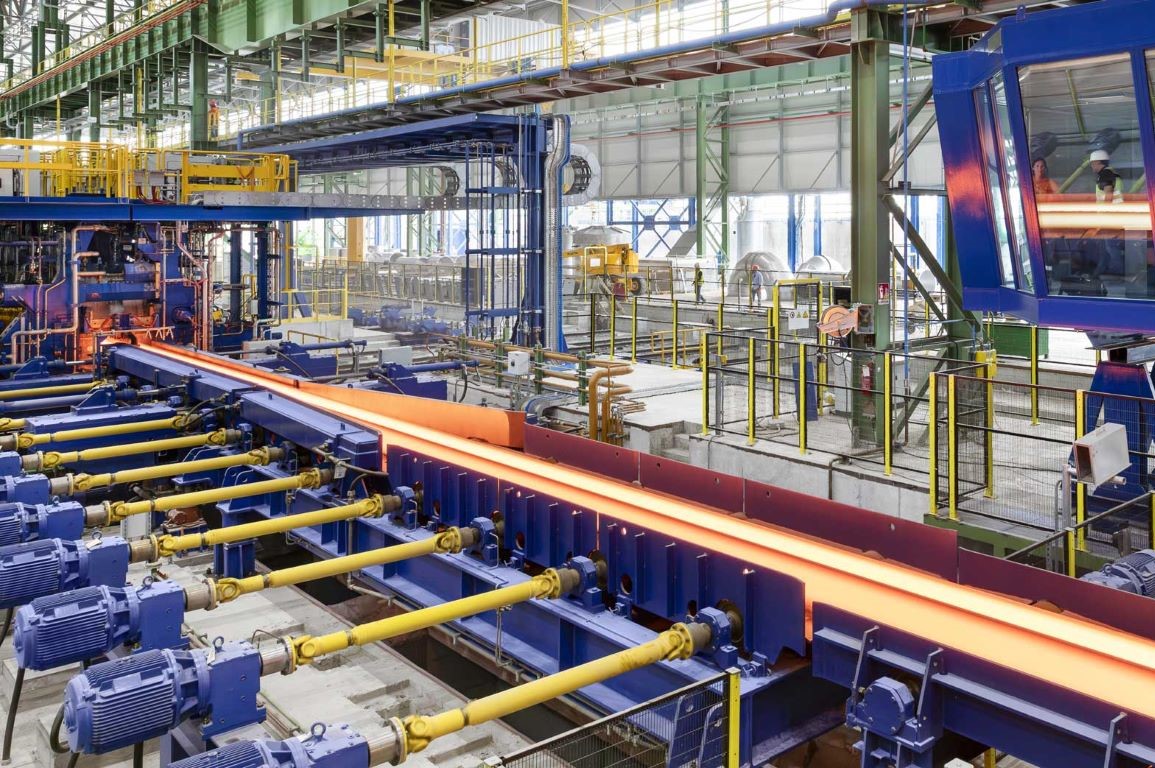
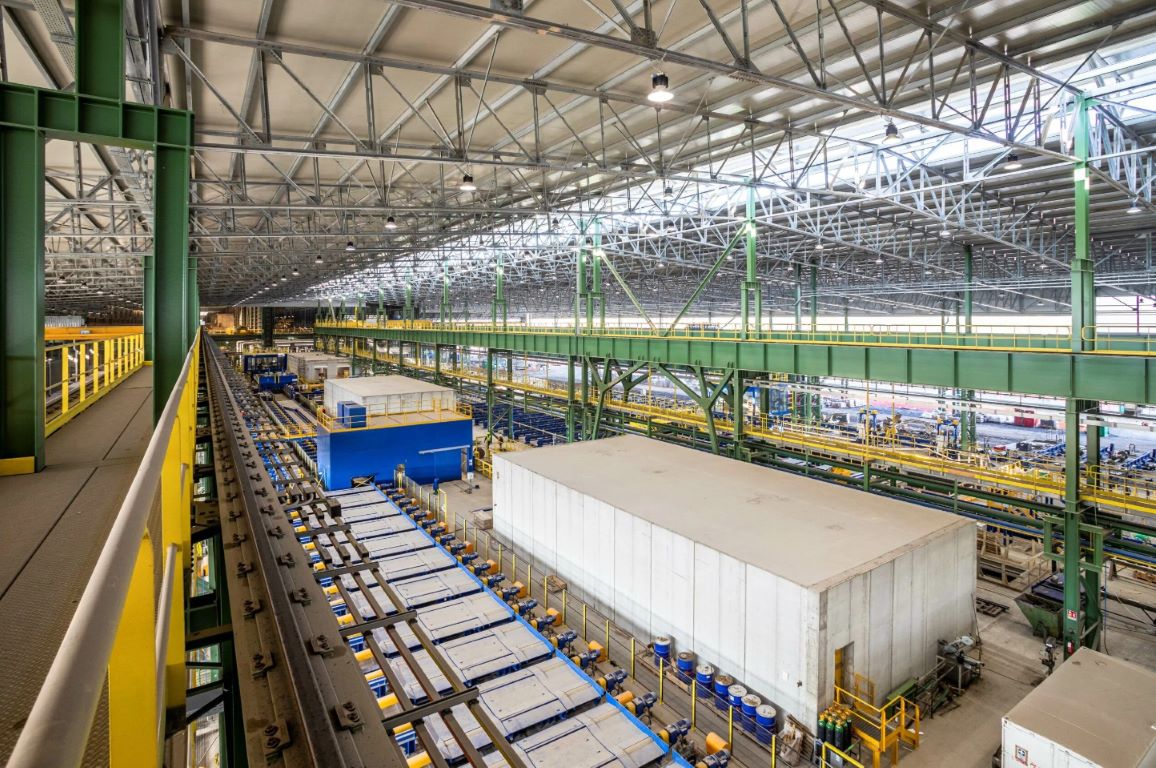
Aunque pueda parecer inusual, las unidades tGard se montaron al revés por factores ergonómicos. Las unidades eran bastante largas, por lo que montar los enclavamientos al revés no solo facilitaba alcanzar los botones (que de otro modo habrían estado demasiado cerca del suelo), sino que también permitía que liberación de escape estuviera a una altura adecuada y cumpliera la normativa.
Las claves del éxito
Nuestro socio de canal LAS ha participado desde las primeras fases del proyecto, trabajando con los jefes de proyecto, los ingenieros y el constructor de la línea, proporcionando recomendaciones sobre las soluciones Fortress y diseñando los puntos de acceso y las lógicas a aplicar.
Fortress era capaz de proporcionar productos únicos para satisfacer la demanda del cliente que nadie más podía ofrecer. Además, la posibilidad de disponer de una mezcla de sistemas mecánicos y electromecánicos (según el área o la aplicación) y obtenerlos del mismo proveedor fue una gran ventaja y una de las claves del éxito.
El cliente estaba familiarizado con Fortress puesto que nuestras soluciones ya se utilizaban en otros sectores de la planta siderúrgica. Conociendo la robustez y la resistencia a condiciones duras, el cliente solicitó que se instalaran productos Fortress en la nueva planta para proteger a 150 trabajadores. Durante más de veinte años, Fortress ha sido el proveedor de referencia para la industria siderúrgica y no cabe duda de que el enfoque utilizado para este tren de laminación podría reproducirse en otras instalaciones.
¿Quiénes son Duferco?
El Grupo Duferco es líder mundial en producción de acero, energía
transporte e innovación.
El nuevo tren de laminación en el que trabajó Fortress está integrado con la
acería, mediante tecnologías innovadoras y sostenibles.
Haciéndose eco de nuestros valores empresariales de ser los innovadores y
objetivo de cero emisiones netas para 2040. Duferco invirtió 220 millones de euros y
y creó 150 nuevos puestos de trabajo con su nuevo tren de laminación Smart Beam Manufacturing.
que tiene una capacidad de producción potencial de 700.000
de 700.000 toneladas al año. La planta tendrá el menor
impacto ambiental posible y funcionará con energía
de fuentes renovables.
Es una oportunidad fantástica para elevar la fabricación de acero en
Italia y Europa a un nuevo modelo sostenible.
Trabajar en estrecha colaboración con LAS
Con más de 30 años de experiencia en el mercado de la automatización y la seguridad industrial, LAS A&S SRL representa un centro técnico comercial en Italia para todos los profesionales de la seguridad.
Como nuestro Channel Partner, LAS representa a Fortress en Italia en todos los
proyectos y han hecho crecer nuestra marca de forma increíble. LAS apoya
a sus clientes desde la identificación de la mejor solución
hasta la asistencia postventa, pasando por el diseño y la implementación
de estos sistemas de vanguardia.
Para cualquier pregunta relacionada con la seguridad en Italia, póngase en contacto
con Fortress o LAS directamente.