Safety Solutions for a Global Steel Manufacturer
For over two decades, Fortress Safety has been working closely with Tata Steel to protect the personnel at their sites. Tata Steel is among the top global steel producers and is the largest steelmaker in the UK.
The Llanwern site is in Newport, South Wales, where steel is produced for UK and European markets. One of the main operations here is the cold rolling and galvanising of metal strips, taking place at the ZODIAC (Zinc and Other Developments in Alloy Coatings) line. Each year, Llanwern produces around 600,000 tonnes of finished product which is used for a variety of constructions and automotive applications.
Watch our video below about the safety solutions at Tata Steel Llanwern
Addressing Safety Challenges on the ZODIAC Line
Cold rolling and galvanising of steel strips are essential processes in steel manufacturing, but they involve several risks for personnel when operating or accessing machines. Over the years, Fortress has helped Tata Steel address various challenges ranging from access control to the enforcement of sequences over large distances, and the management of permissions.
Welding – At the entry section, the coils are fed onto the line and welded together, forming a continuous strip. Fortress interlocks are used to allow access when operators need to enter the safeguarded space for minor interventions such as changing weld wheels or removing scrap cuts.
Entry Looper (Accumulator) – This section extends over multiple levels and manages the flow and tension of steel strips when a new roll enters the system, maintaining a continuous and controlled feed. Previously, there used to be fixed guards that operators would remove during maintenance tasks. However, over time this can lead to damaged guards and expose personnel to hazards if guards are not properly re-bolted.
These challenges have been addressed by upgrading with Fortress mechanical trapped key systems. Turning the first key triggers a stop, and a key exchange device is then used to release the keys that allow to open the interlock devices on the upper levels where the sliding guards are situated. Another advantage of this solution is that by using mechanical interlocks it is possible to reach areas where wiring is impractical.
Main Furnace – Before entering the zinc bath, the steel strip passes through a furnace where it is heated at high temperatures. There is a gas hazard since personnel can be exposed to various dangerous gases, and to be allowed in the area a gas awareness training is needed.
A FRANK system is used not only for access control, but also to manage authorizations. Employees can use their RFID cards to request access, and only those with the right permissions and up-to-date gas awareness training are allowed in. The integration of training and access permissions prevents unauthorised access and creates a data log which captures access requests.
Automotive Finishing Line (AFL) – This dedicated inspection line receives the galvanised coil. In some circumstances personnel need to perform a visual inspection of the strip. amGardpro interlocks allow access to the area by stopping the strip before access is allowed. Once the inspection is complete, a manual reset can allow to restart the line.
Conclusions and Future Perspectives
We are proud to have developed a strong relationship with Tata Steel, being entrusted for over 20 years with protecting personnel at their sites. Fortress has addressed a range of challenges involving different access conditions and requirements for various processes on the Zodiac line. We look forward to continuing working together and bring our safety solutions to other parts of the plant as well as other Tata Steel sites.
Case Study Gallery
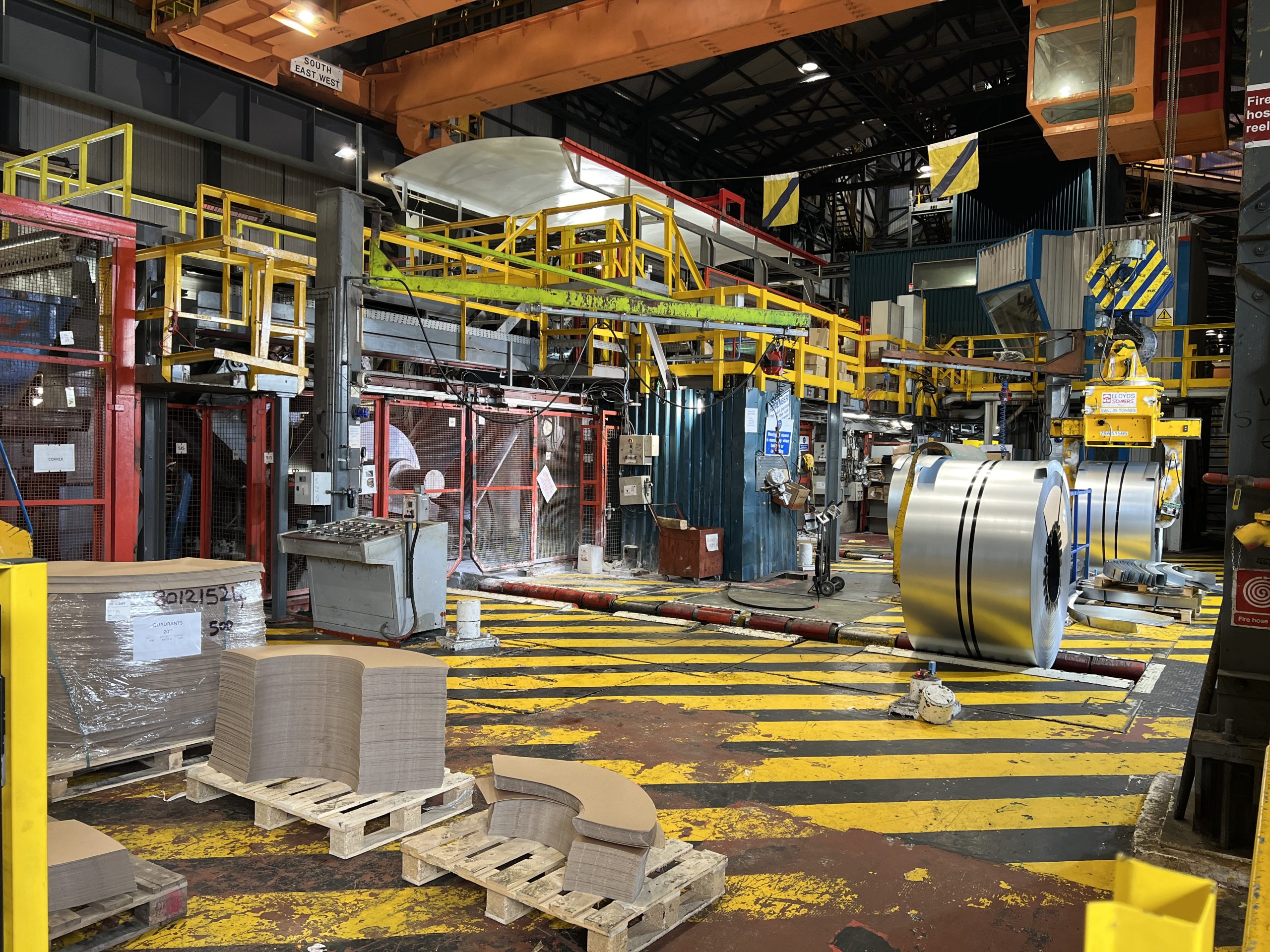

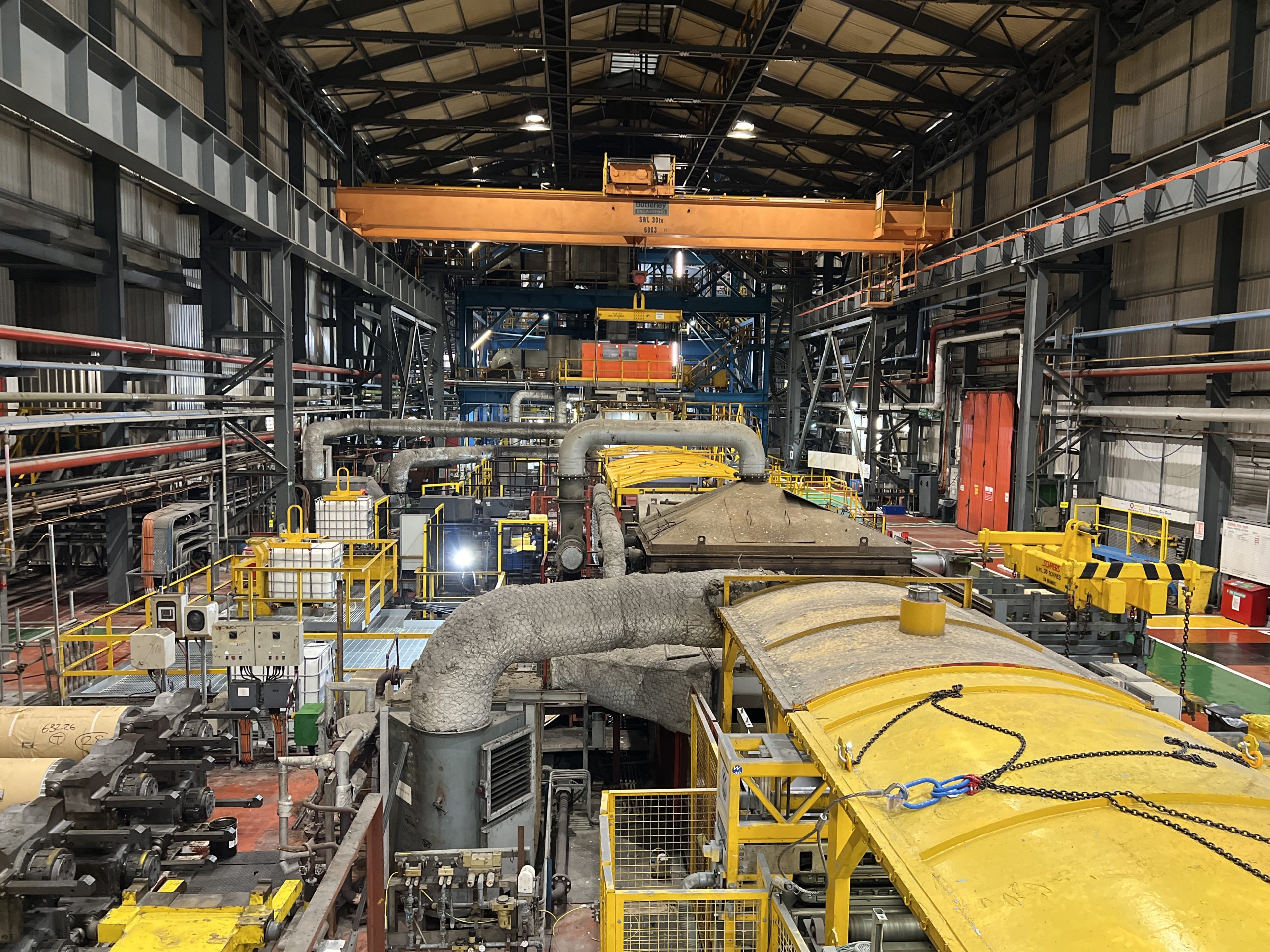
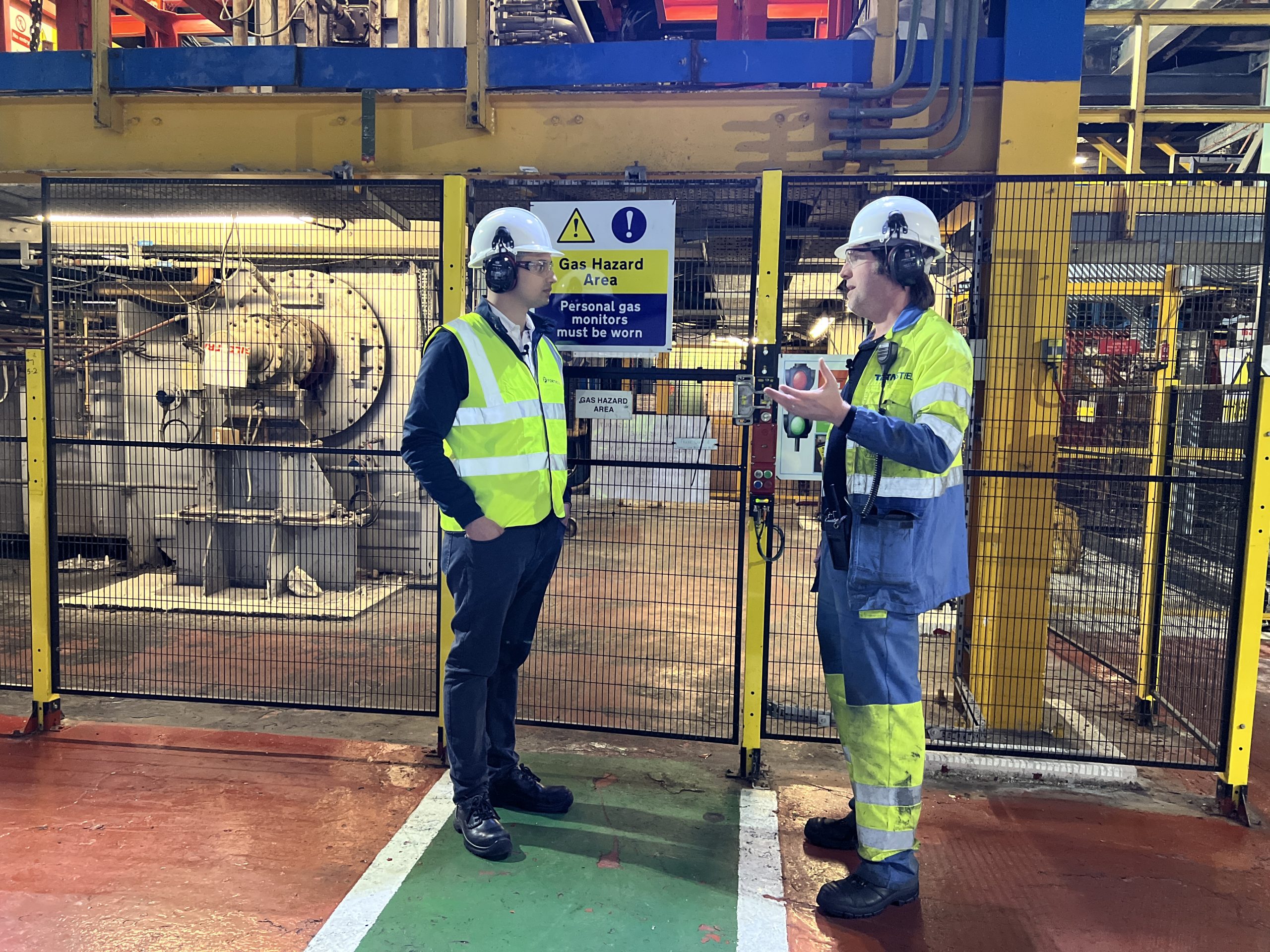
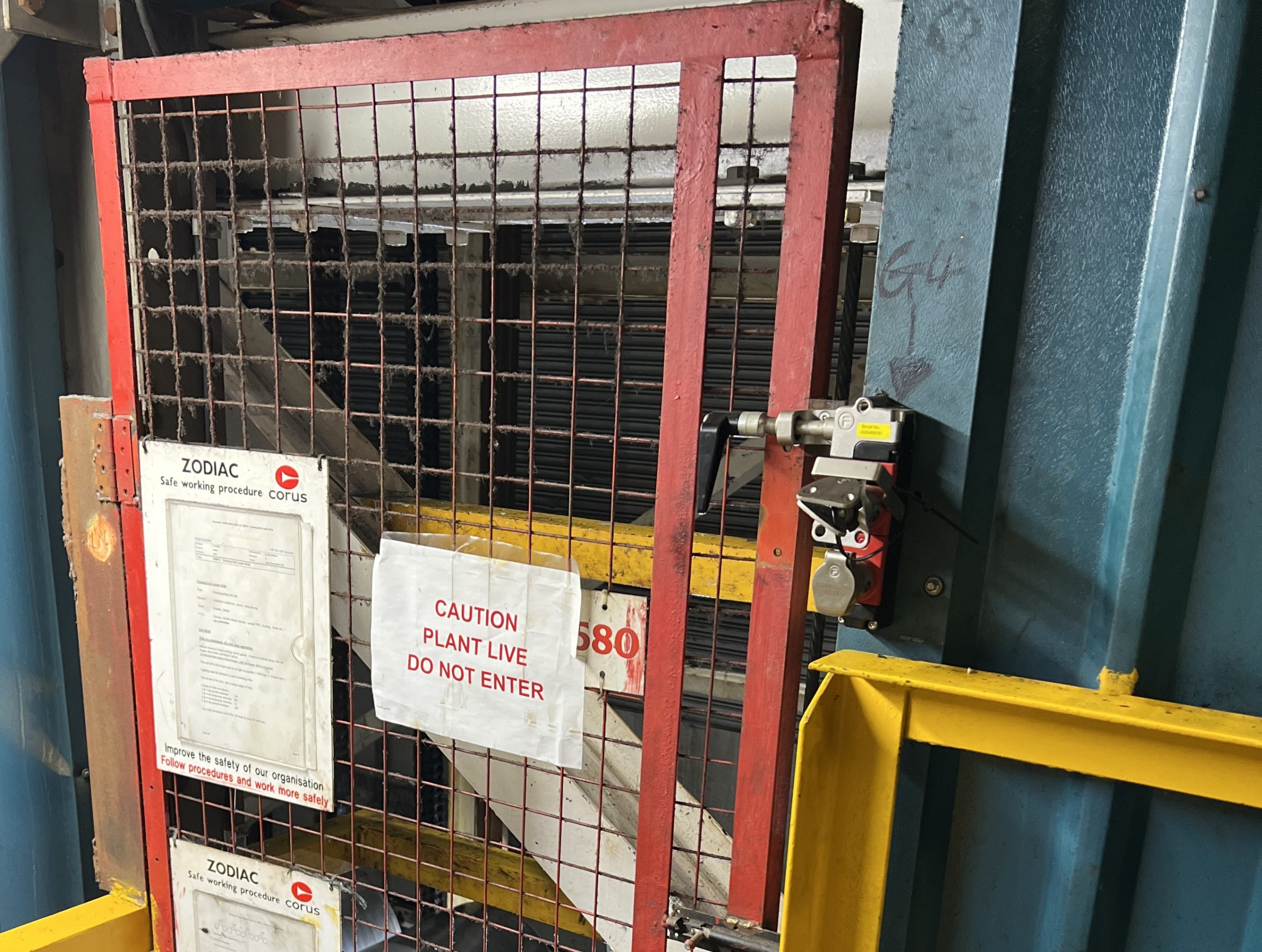
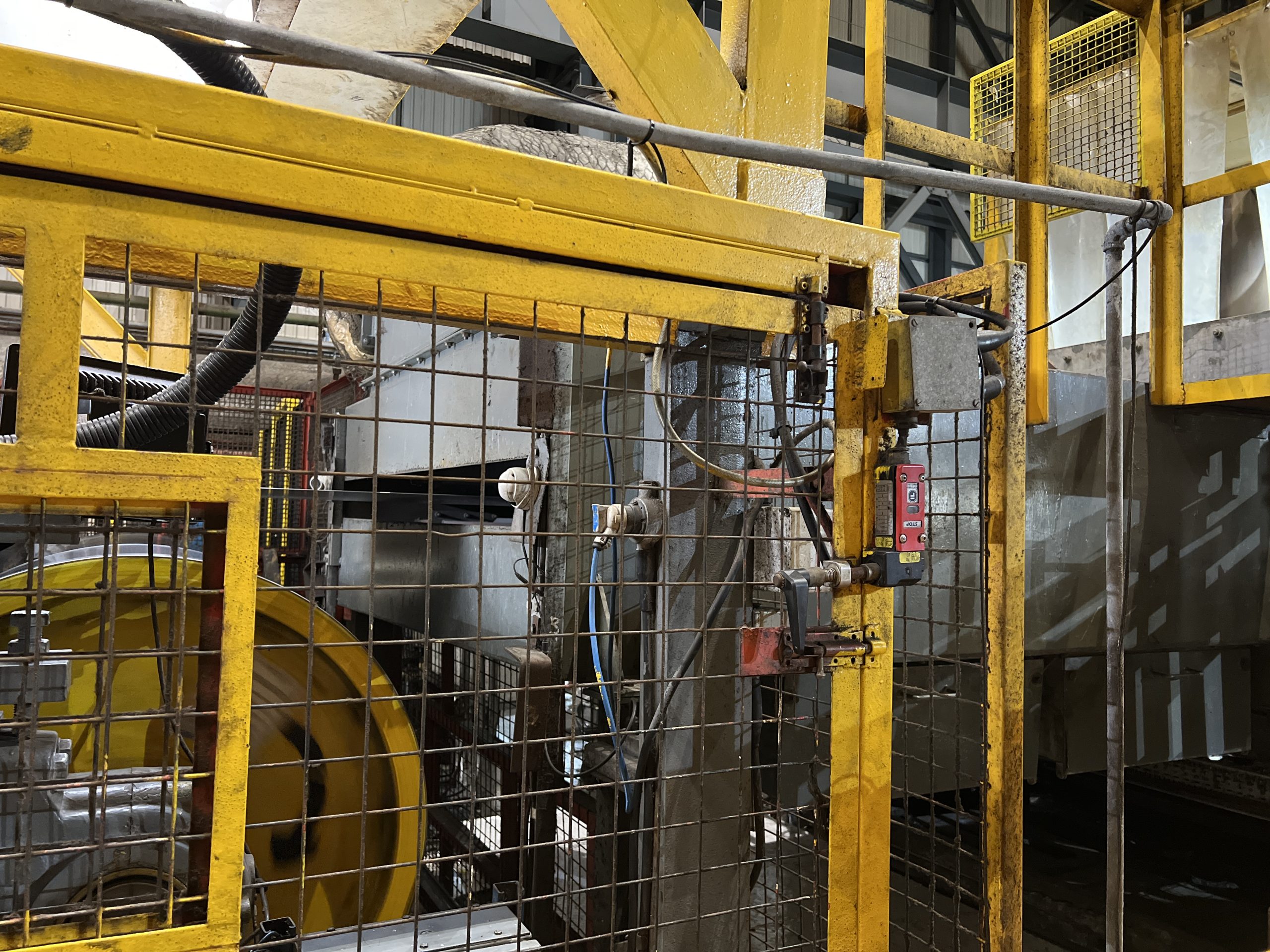
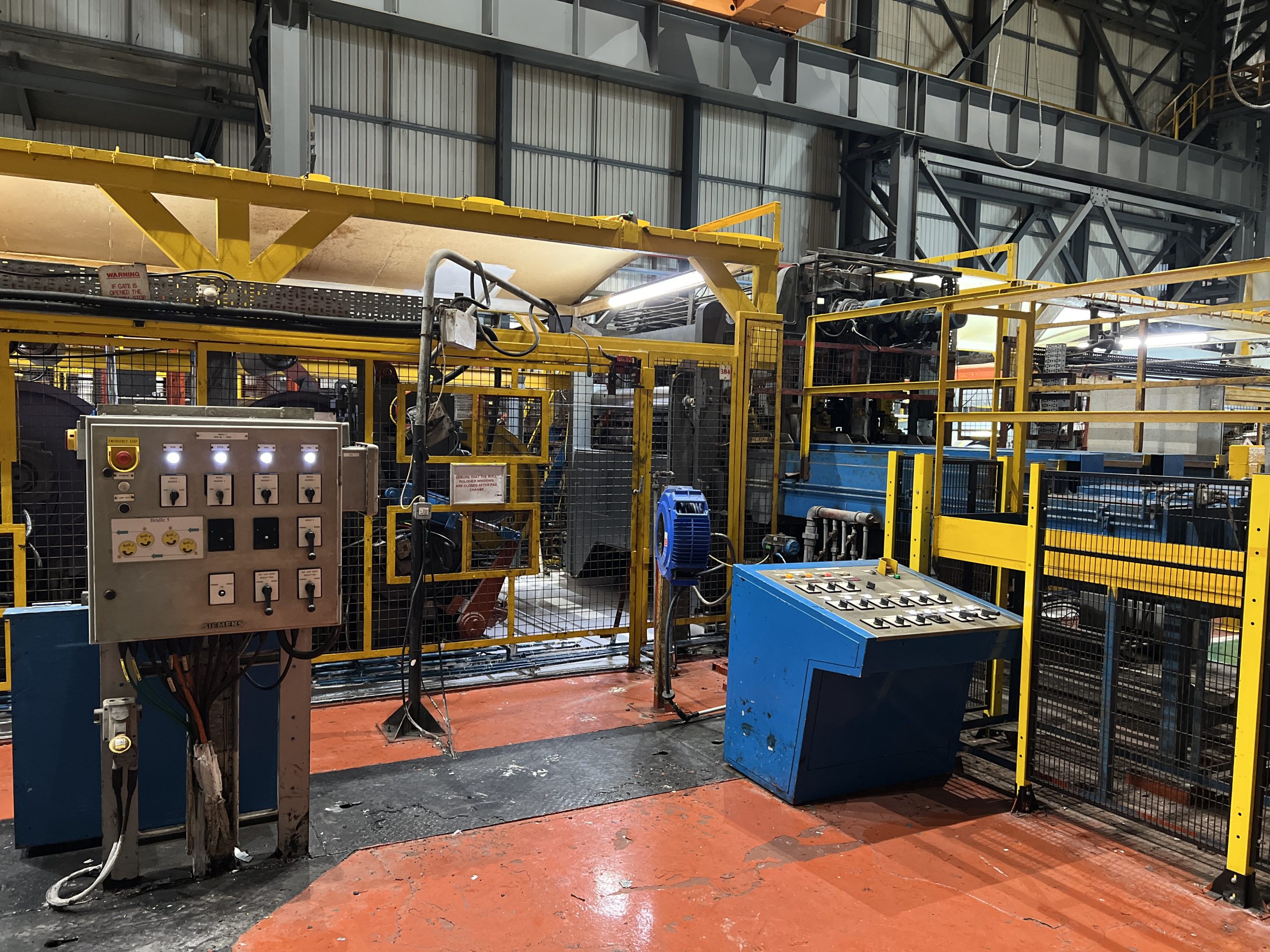
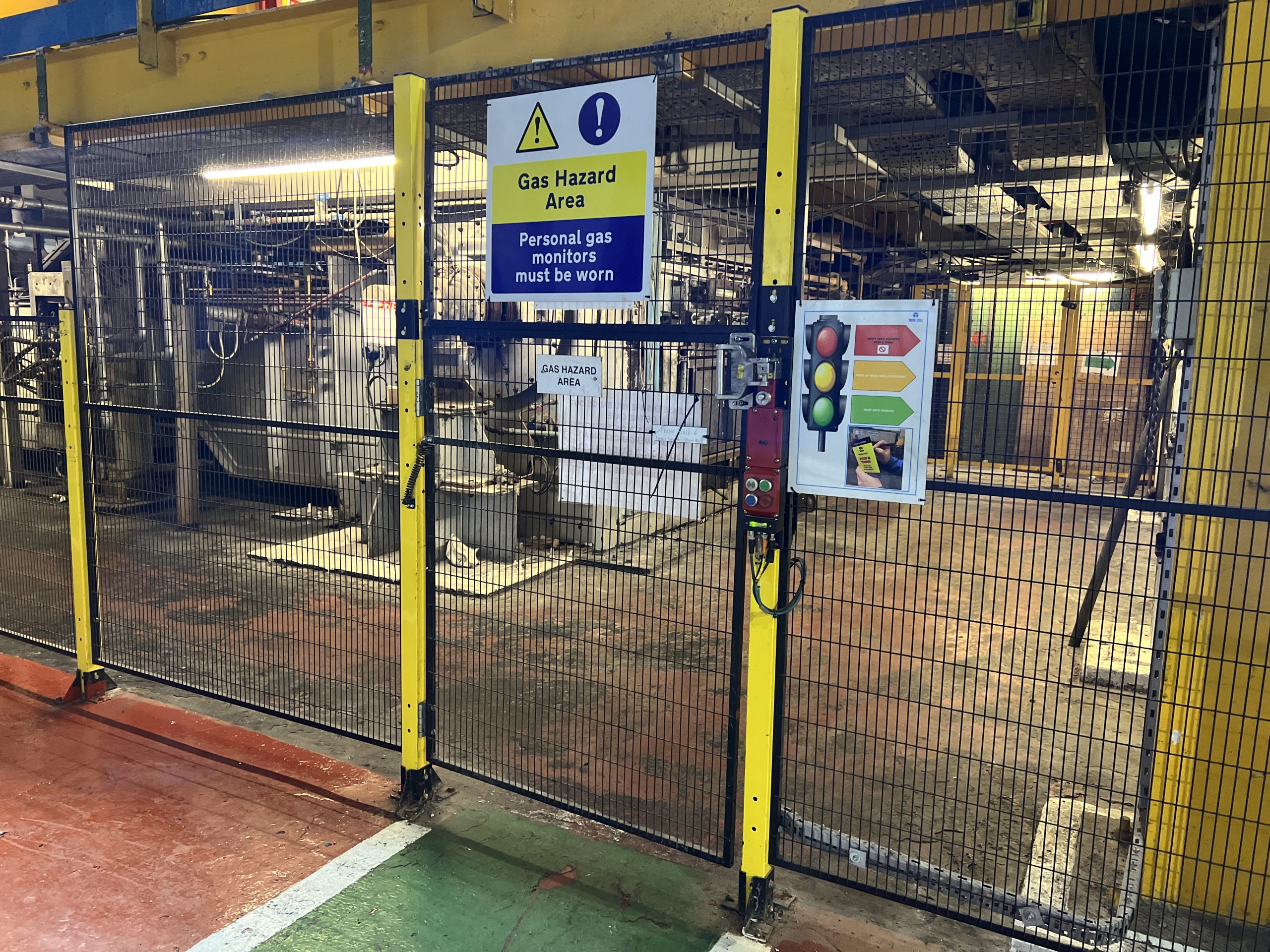