The Importance of Enforcing Access Permissions
In the manufacturing industry, ensuring that only authorised personnel perform specific tasks is essential for both safety and productivity. Unauthorised access can in fact expose workers to hazards and disrupt operational efficiency.
It is not always possible to simply rely on training plans to prevent unauthorised personnel from entering safeguarded spaces or operating controls. Enforcing personnel authentication and permissions as part of controlling access not only can help reduce risk, but also contributes to reducing unnecessary downtime.
Tata Steel Llanwern (Newport, South Wales, UK) has chosen the Fortress FRANK system to manage personnel permissions and control access to certain areas of their ZODIAC line, which is where the cold rolling and galvanising of metal strips takes place. Over the years, this solution has helped Tata Steel enhance safety and improve their processes.
FRANK in a Nutshell
Designed to work with proNet – the network communication module of the amGardpro range – the FRANK industrial access control software manages permissions for machine control or access. FRANK works with existing RFID cards used on site and logs interaction events including date, time, and frequency, providing data insights that can support efficiency and productivity analysis, identify irregularities, and optimise processes.
The Importance of Enforcing Access Permissions
One of the areas where Tata Steel implemented FRANK was the direct fire section (DFS) of the main furnace, where steel strips are heated to high temperatures before entering a zinc bath. Personnel can be exposed to dangerous gases such as hydrogen, nitrogen, and natural gas, hence, to be authorised in the area a mandatory gas awareness training is needed.
The access system previously in place involved using a key attached to a gas monitor, so that operators could only enter the gas hazard area if they had a gas monitor with them. However, such a system did not differentiate between personnel with up-to-date or expired gas awareness training. The customer decided to adopt the FRANK system from Fortress Safety as it can link the access permissions to the training status.
The solution used by Tata Steel consists of an amGardpro interlock, featuring a proNet module for network connectivity, RFID card reader, and escape release. Inside the safeguarded space there is also a control pod with another RFID reader that operators use to badge out when leaving the area.
Only employees with the right permissions and up-to-date training are allowed access to the gas hazard area. The integration of training and access permissions with FRANK prevents unauthorised access and creates a data log which captures access requests and user interactions.
Enhancing Access Control to the Drossing Robot Area
FRANK was also implemented in the area safeguarding the pool pit, which is where the heated steel strip enters the zinc bath. Here, a drossing robot is used to remove dross from the surface of the molten zinc.
Previously, access to this area was managed manually via a whiteboard system where personnel would sign in and out. However, this approach did not track who accessed the area and relied on people filling in the board correctly. With the FRANK system Tata Steel now has a live update status on who is in the pot area, and most importantly, ensures personnel is authorised to do so.
When designing this solution, there were considerations around reducing cabling and installation. Particularly, for the drossing robot area Tata Steel decided to use Power over Ethernet (PoE). Having a single cable for each interlock facilitates the installation and maintenance processes and helps minimise cabling on the floor (particularly useful considering the hazards related to zinc).

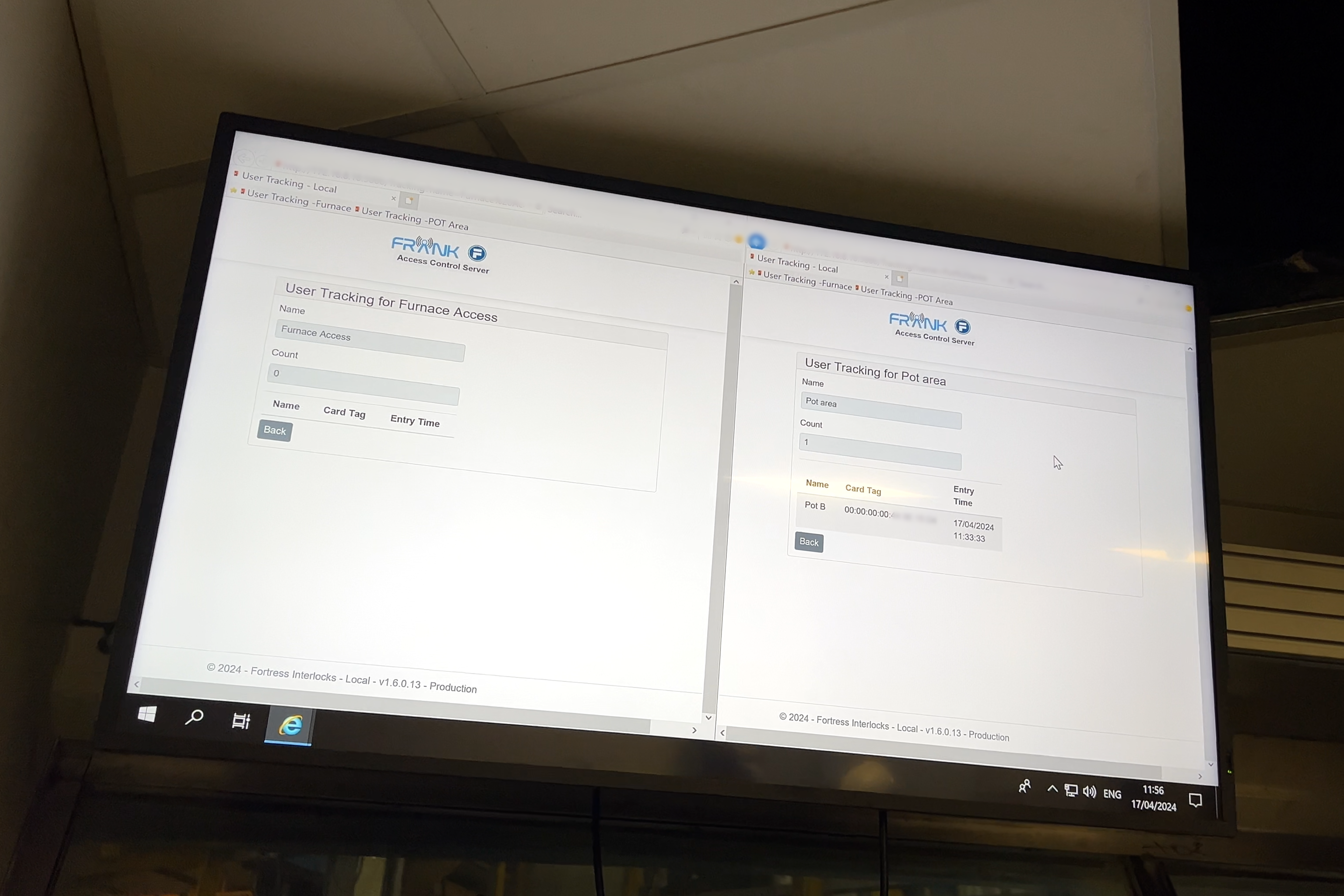

The Key to Success
The implementation of FRANK offered the customer several advantages. Tata Steel has been able to make sure that only authorised people with up-to-date training records are granted permissions and allowed access to certain areas.
The decision to adopt FRANK from Fortress was influenced by several factors, including:
Improved procedures
This solution offers better access control compared to previous protocols
Real-time data availability
The ability to log and display interaction data in real time allows teams in the control room to monitor activities and take immediate action if needed
Scalability
FRANK can easily be expanded to additional areas as needed
Compatibility
The system works with the existing RFID cards already used on site, simplifying integration
In addition, FRANK offers valuable insights through its data logs. By analysing user interactions, the system helps optimise access control processes.
Tata Steel’s partnership with Fortress Safety has significantly enhanced safety and access control at their Llanwern site. With the FRANK system initially implemented in the furnace and pot areas, the customer plans to expand its use to other parts of the plant, continuing to improve safety and operational efficiency across the facility.
Read more
Part 1 of our Tata Steel case study explores a variety of challenges, including access control to the enforcement of sequences over large distances. The solutions we also provided include: