Conveyors are a key component of many warehouse automation systems, helping to quickly and efficiently move goods throughout the facility. However, as with any piece of machinery, it’s important to prioritize safety when using conveyors. In this article, we’ll delve into the importance of conveyor safety, including common hazards and safety tips, as well as specific machinery safety standards and how interlocks can help comply with these standards.
Common Conveyor Hazards
Conveyors can present a number of hazards to workers, including moving parts, electrical components, and the risk of falling or being struck by objects. It’s important to identify and mitigate these hazards to prevent accidents and injuries. Some common conveyor hazards include:
Entanglement
Workers can get caught in the moving parts of a conveyor, potentially leading to serious injuries or even death. It’s important to keep loose clothing and long hair away from conveyors and to use guards and barriers to prevent entanglement.
Electrical Shock
Conveyors may have electrical components that can present a shock hazard if they’re not properly grounded or maintained. Workers should be aware of these components and take precautions, such as wearing protective equipment and avoiding contact with electrical components when possible.
Falling Objects
Conveyors can sometimes move heavy or awkward objects, which can present a risk of falling and causing injury. It’s important to secure items on the conveyor and to maintain good visibility to reduce the risk of falls.
Struck-By Accidents
Workers can be struck by falling or moving objects on a conveyor, such as boxes or equipment. It’s important to maintain good visibility and to stay clear of conveyors when they’re in operation to reduce the risk of struck-by accidents.
Safety Tips for Conveyor Systems
To keep workers safe around conveyors, it’s important to follow some basic safety guidelines:
- Guarding: One of the most effective ways to prevent conveyor accidents is to use guards and barriers to keep workers away from moving parts. This can include fixed guards around conveyor belts and other moving components, as well as barriers to prevent workers from accessing dangerous areas.
- Training: Proper training is crucial for keeping workers safe around conveyors. This should include information on the proper use of the conveyor, as well as how to identify and mitigate hazards.
- Maintenance: Regular maintenance is important for ensuring that conveyors are in good working order and operating safely. This can include checking for wear and tear, replacing damaged parts, and ensuring that electrical components are properly grounded and maintained.
- Interlocks: Interlocks are a useful tool for ensuring that conveyors are only operated when it’s safe to do so. These systems can be used to stop the conveyor when, for example a worker enters a hazardous area to conduct a task.
The Importance of Complying with Safety Standards
Adhering to safety standards is crucial for preventing accidents and injuries in the workplace. When it comes to conveyor systems, following safety standards helps to ensure that the machinery is designed and constructed in a way that minimizes the risk of accidents. It’s also important to regularly maintain and inspect conveyors to ensure that they’re in good working order and operating safely.
Statistics on Conveyor Injuries
According to data from the U.S. Bureau of Labor Statistics, conveyors were involved in 4,881 non-fatal injuries in the workplace in 2019. These injuries ranged from lacerations and fractures to sprains and strains, and could have been prevented with proper safety measures in place.
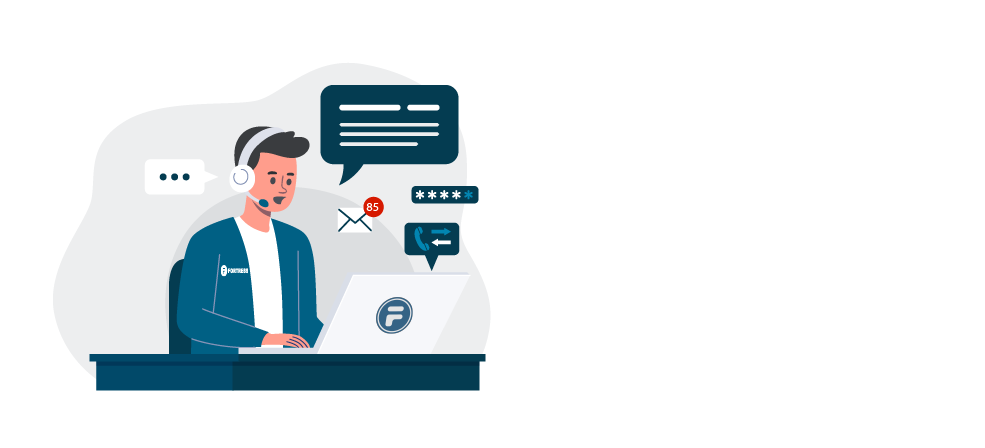
Fortress Safety has a team of application experts who can help you.
If you're responsible for the safety of conveyor systems in your facility, you may need help ensuring that you're complying with all relevant safety standards and best practices.